QxAutomation-Manager is a turn-key solution to interface between Ethernet based industrial automation hardware and your CMM that’s running CMM-Manager. This Windows Application allows control of CMM-Manager software in a typical industrial automation cell containing a robot and/or PLC. The automation application can launch CMM-Manager application, calibrate probe tips, send machine to safe load / unload location (home), launch inspection program(s), monitor program running status, monitor robot safe position, report errors from CMM-Manager, report pass / fail status of dimensional report and much more.
QxAutomation-Manager is designed to be easy enough for the end user to setup with their own collaborative robot yet comprehensive enough for an industrial integrator to work with their preferred robot or PLC. Integrations ranging from machine tending with a single robot to a full integration within a manufacturing cell is possible with our turn-key solution.
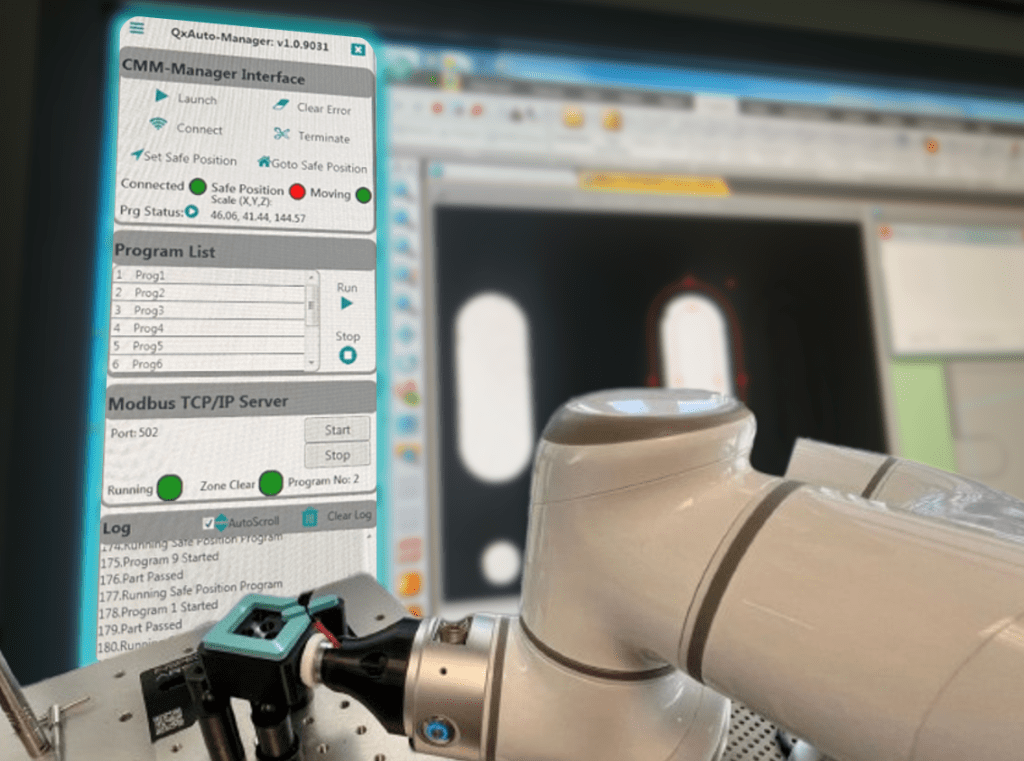
Available Ethernet Protocols
- Modbus TCP/IP Server
- Modbus TCP/IP Client
- Traditional Modbus (Coils & Registers)
- Modbus (Fanuc specific) – learn more
- Holding Registers Only (Siemens)
- Socket TCP/IP
When should I consider automation?
🔁 You inspect high volumes of similar parts
- Robots shine in repetitive, consistent workflows. Think pallets of castings, machined blocks, or injection-molded parts.
🌙 You’re aiming for lights-out or unattended shifts
- Pairing a robot with a CMM allows 24/7 inspection – ideal if you’re scaling or chasing labor efficiency.
📦 You want to reduce manual handling
- Robots reduce human error in part placement and ensure consistent loading, which improves measurement repeatability.
🔗 You’re integrating with other automation
- If your machine tools already have robotic loaders, it makes sense to bring the CMM into the same automation loop (full closed-loop inspection and part handling).
Legacy Discrete I/O Support
Migrate easily from the legacy Nikon Metrology / National Instruments ioMonitor solution. We’ve created a turn-key solution to migrate from legacy discrete I/O (+/- 48v) to this modern Ethernet based solution.