CMM-Manager 2024 introduces several enhancements aimed at improving measurement efficiency, accuracy, and user experience.
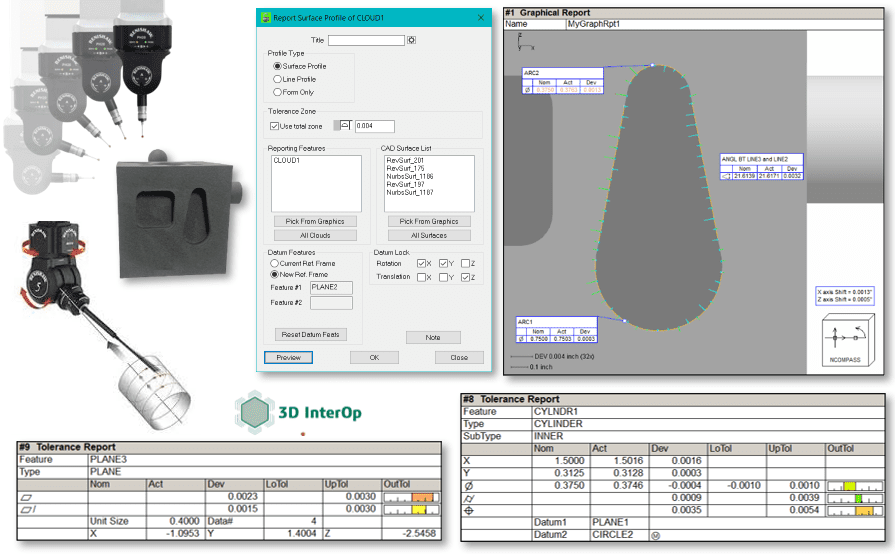
The key new functionalities in this release include:
🧭 PH20 and 5-Axis Motion Enhancements
Expanded support for Renishaw PH20 heads and 5-axis motion systems, enabling faster and more flexible measurement strategies for complex geometries.
🎯 Tip Calibration Improvements
Refinements to the tip calibration process enhance accuracy and reduce setup time, ensuring reliable measurements across various probe configurations.
📈 Scanning Enhancements
Improved scanning capabilities provide more precise data capture, benefiting applications that require detailed surface analysis.
📊 Profile and Reporting Enhancements
Upgrades to profile measurement tools and reporting features offer more comprehensive analysis and clearer presentation of results.
🗂️ Improved CAD Import Options and Speed
Optimizations in CAD import functionality allow for faster loading and better handling of complex models, streamlining the preparation phase of inspections.
🛠️ New Shop Floor Launcher Functionality
The introduction of a Shop Floor Launcher facilitates easier program execution on the shop floor, enhancing usability for operators and reducing the potential for errors.
These updates are designed to streamline inspection workflows and support advanced measurement tasks. For a comprehensive overview of all new features and enhancements, you can refer to the official release notes:
Version 2024 (12.4.1.9770)
Release Date: 12/20/2024
Required SSC Date: 01/01/2025 or later
1. Supported Operating Systems
- Windows 11 Pro or Enterprise
- Windows 10 Pro or Enterprise
* Windows 7 or 8 may still work, but not officially supported or tested
* CAD Converter 2023 and later no longer support 32-bit OS, but CAD Converter
2022 can be used with CMM-Manager 2024 on 32-bit OS
2. Language Support
- English, Chinese, Czech, French, German, Italian, Japanese, Polish, Spanish
3. CAD Importer Support: Spatial 3D InterOp Release 2025 1.0
- The following formats and their versions are supported:
* ACIS R1 – 2025 1.0
* CATIA V4 4.1.9 - 4.2.4
* CATIA V5/V6 V5 R8 – V5-6 R2024
* DWG 2.5 – 2025
* Inventor V6 – 2025
* JT JT 8.x, 9.x, 10, 10.2, 10.3, 10.5, 10.6, 10.7, 10.8 and 10.9
* NX NX 1 – NX 2406
* Parasolid 9.0.x – 37.0.x
* Pro/E 16 – Creo 11.0
* Solid Edge V18 – SE 2024
* SolidWorks 2003 – 2025
* STEP AP203, AP214, AP242
* VDA-FS 1.0 – 2.0
4. Profile Reporting Enhancements
- Integrated Cloud-to-CAD into Profile reporting
- Addes support for more comprehensive datum configuration
- Added support for floating datum by using datum locks and the default locks
are auto determined based on datum configuration
– Added option to use a total tolerance zone and removed Distribution option
5. Other Reporting Enhancements
- Added support for Flatness per unit tolerance
– Added user preference to use GD&T symbol instead of text for tolerance name
- Added support for constrained best-fit in Report Cloud-to-CAD and Cloud-to-Curve
- Added option to invert best-fit transformation in Report Cloud-to-CAD and Cloud-to-Curve
- Added option to show Max and Min deviation text box in graphical report
- Added option to show 2D best-fit info text box in graphical report
- Added option to show Ncompass in graphical report to depict best-fit result
- Added option to display dev. value and sequence number for dev. labels in graphical report
- Added min/max suffix to dev. labels in "Display dev. value" mode
- Added option to toggle on/off all report output during program execution
- Added support for .xls and .xlsm file formats in Excel to CSV command
- Allows printed header even when report header output is disabled
6. Tip Calibration Enhancements
- Made Locate Cal. Sphere operation programmable (for non-I++ systems only)
- Batch Tip Calibration
- Added option to force "Establish Ref. Tip" at beginning of calibration
- Added option to only calibrate tips suitable for a specified cal. sphere
- Added user preference for table clearance distance for tip calibration
- Improved tip calibration routine to avoid possible collision when using the
lower half of cal. sphere with short stem
7. PH20/5-Axis Measurement Enhancements
- Allows using 5-axis commands for measuring circular plane
- Allows centroid of range adjust for circular plane to exceed surface edges
- Uses more accurate approach and backoff position for creation, display and
simulation of PH20 link paths
- Improved PH20 link path efficiency for Hole Pattern
- Eliminated unnecessary ceiling moves from PH20 paths
- Fixed: PH20 path planning and display issues with multiple probe assemblies
- Fixed: Link path for PH20 measured cloud could cause software crash
- Fixed: Link path could change measurement mode from PH20 to PH10 silently
- Fixed: Surface edge could not be measured with PH20 probe
- Fixed: PH20 might fail to go outside of safe cube when OP Planner was Used
- Fixed: Performance issue when creating PH10 paths using PH20 in a large program
8. Scanning Enhancements
- Added disc probe support for SP25 scanning on non-UCC controllers
- Added new measurement methods (Lines, Circles) to Scan Cylinder
- Added option to define helical scan by specifying pitch
- Added new Scan Point command using self-centering function (I++ systems only)
- Added Pick Apex tool to Scan Sphere
- Fixed: Scan path should be based on actual reference frame instead of nominal
- Fixed: Simulation speed of circle scan was not consistent
- Fixed: Stop plane orientation (display) of 2D open scan might not be accurate
9. CAD Import and Management Enhancements
- Allows grouping CAD entities into layers by color
- Added new secondary healing option for CAD import
- Added pre-process option for importing DXF file
- Added option to move entire part program with Place CAD command
- Added new Pick to Select tool to CAD Editor
- CAD clouds are now highlighted when selected in CAD Editor
- Fixed: CAD import preferences were not migrated
10. Shop Floor Launcher Enhancements
- Added Calibrate Rotary Table command in SFL
- Keeps SFL open, if open, when executing program from command line
- Fixed: SFL did not handle tall pictures correctly
11. Other Enhancements
- [1] Improved robustness of QxAutomation-Manager for extended runs
- [2] Added new VBScript functions: GetReportHeaderInfo, GetCloudPointName, GetDatumAlignIterationCount
- [3] Added option to project edge point to sample hit height
- [4] Added option to define sphere apex by IJK input in addition to picking
- [5] Updates nominal coordinates of features used in Bestfit Alignment based on user input
- [6] Ensures Enter key and joystick OK button always work on Prompt dialog
- [7] Added tool to export points from measurement dialog
- [8] Added support for more image file formats in various operations
- [9] Recall Reference Frame command now highlights currently selected ref. frame in graphics
- [10] Allows Get Probe Assembly operation to be copied
- [11] When an operation is enabled/diabled, dependent operations will be enabled/disabled automatically
- [12] Added support for using ACR1 rack in passive mode
- [13] Added option to allow calibrating ACR1 rack without using datum stylus
12. Driver Updates
- Mitutoyo UC
- Fixed: SP25 calibration result incorrect when scale factor was not 1.0
- Pantec
- Fixed: SP25 DCC touch measurement following scanning did not work
- Renishaw Equator
- Fixed: Could not connect to older Equator Server running on Win7 system
- Sheffield MP/SMP
- Allows to configure the RECORD joystick button as keyboard Return for Prompt
- Fixed: Calibrate Probe Head command not working
- Fixed: Rotary table accuracy issue when table axis was tilted
- Fixed: Rotary table center was not retrieved correctly in INCH mode upon connection
- UCC Direct 2.0
- Added rotary table support
- UCC I++
- Added the ability to execute ReQualify Head from Machine Setup
- Fixed: Cylindrical probe and disc probe may not sync correctly
- Zeiss C99
- Fixed:No trigger received from C99L Controller
13. Bug Fixes
- [1] Touch speed should be used for moving into the feature for Find Hole function
- [2] Reordering reporting operations in Program database may dissociate report items
- [3] Batch reporting of true position for cylinders did not use correct vector
- [4] 2D scan cloud offline resulted in empty cloud in Teach mode
- [5] Line/Plane option update issue on the Distance Between dialog
- [6] Failed to set password in Preferences > General Permission on some PC's
- [7] Circular planes would not export as IGES
- [8] Circular planes added to CAD were not recognized as circular plane
- [9] Report item title and report header should always be left-justified
- [10] Hole Pattern path disappeared from graphics display after Save
- [11] Circular Runout name "CRUN" in report could become Total Runout "TRUN"
during program run if the operation was in a collapsed program group
- [12] Could not add/modify points when rectangular 5-Axis touch was selected as default
- [13] Software crash if using variable feature name in Report Profile and Cloud-to-CAD
- [14] 5-Axis move inside Add Move/Get Tip may be executed asynchronously when verified
- [15] Save or Auto Save while simulating a hole pattern measurement would cause software crash
- [16] Reset Actuals would clear out all points from an extracted cloud
- [17] Reset Actuals on joystick created/measured features would clear out raw data
- [18] Simplified CAD Measure interface did not create raw data
- [19] Report database did not auto scroll when drag-n-drop items at the bottom of the tree
- [20] Copy & Paste did not work for Report Profile
- [21] Smaller font size displayed on main graphics when CAD or Cloud editor was open
- [22] CMM-M would not restore/maximize once minimized on certain drivers
- [23] Software crash when re-pathing from right click menu on joystick-taught features on PH20
- [24] Software crash when closing the report print preview window
- [25] Gap between probe head and ram due to probe mount offset may cause path collision
- [26] Cloud-to-CAD Report added to program during Align Part if Live Report option was enabled
- [27] ACR1 front direction vector display was incorrect in Probe Station dialog
- [28] Runtime Align Part did not work if a fixture ref. frame was taught and recalled
in the same program
- [29] Opening a .prg file may not load fixture ref. frame
- [30] Revo 5-axis scan path creation would cause nominal shift when nominal and
actual ref. frames are different
- [31] Sweep Scan for plane only contained two raw data points unless verified
--End