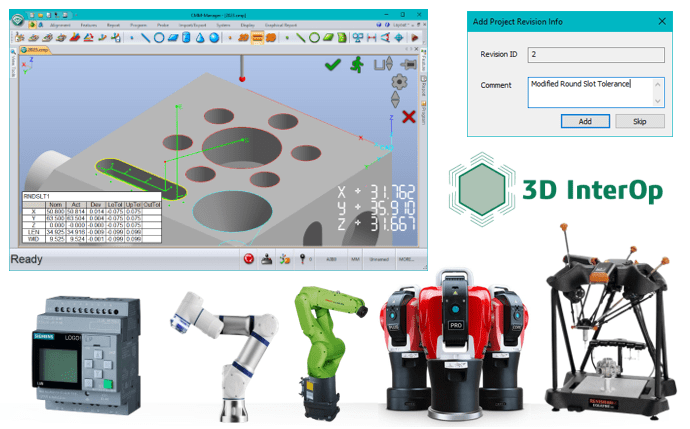
CMM-Manager 2023 HF1
Version 2023 HF1 (12.3.1.9402)
Release Date: 01/11/2024
Required SSC Date: 01/01/2024 or later
General Information
This hotfix release is a full standalone release and will overwrite any existing 2023 installation
Bug Fixes
[1] Error when connecting or homing with IMUSB box
[2] Hole pattern paths deleted after running Operation Plan
CMM-Manager 2023
Version 2023 (12.3.1.9387)
Release Date: 12/22/2023
Required SSC Date: 01/01/2024 or later
1. Supported Operating Systems
- Windows 11 Pro or Enterprise
- Windows 10 Pro or Enterprise
* Windows 7 or 8 may still work, but not officially supported or tested
* CAD Converter 2023 or later no longer supports 32-bit OS, but CAD Converter 2022 can be used with CMM-Manager 2023 on 32-bit OS
2. Language Support
- English, Chinese, Czech, French, German, Italian, Japanese, Polish, Spanish
3. New Automation Software - QxAutomation-Manager
- Simple yet powerful solution for automation integration with CMM-Manager
- Intuitive UI for configuration, testing and operation
- Allows a maximum of 255 programs
- Supported protocols:
- Modbus TCP/IP Server
- Modbus TCP/IP Client
- Generic, Fanuc, Siemens
- Socket TCP/IP Client
4. Added support for Renishaw Equator Gauging System
- Supports full functionalities including CMM calibration for Equator
- Allows one program to be used for calibraiton, mastering and measuring
- Supports VB Script variable for mode selection
5. Added support for API Laser Tracker
- Supports API Radian Core/Plus/Pro models
- Supports various targets including SMR, Nest and vProbe
- Supports auto stability trigger and auto probe comp point collection
- Supports Jog, Go To and Leap Frog operations
6. Usability Improvements
- Added optional simplified CAD measurement interface for quick programming
- Made Program database right click menu context sensitive
- Added shortcut keys in the Program database for Copy, Paste, Cut, Find, Select All
7. Reporting Enhancements
- Allows to add report notes from Report database right click menu
- Allows multi-select Cloud features for Report Cloud Operation - Allows to include header and customer data fields at top of each report page
- Allows output of report title in DDE operation
- Allows to expand/collapse all report database window - Changed report preview display to higher contrast colors
- Improved drag-n-drop behavior in Report database
- Auto switch to Report database when creating a new graphical report
- Fixed: buildup of background Excel instances caused issue with paste address function in DDE operations
- Fixed: dashed lines for tolerance band did not show correctly in graphical report
- Fixed: Distance and Angle Between batch reporting only applying nominal values to first report output
8. Path Planning Enhancements
- Increased default clearance distance for path planning to 6.0 mm
- Added preference for rectangular vs circular for 5-axis plane measurement
- Fixed: link path issue in certain cases
- exit point from previous feature was too far out than needed
- Fixed: Verify did not create approach path if the first command was a 5-axis move
- Fixed: find Hole paths for Relative Measure could be created on wrong side of the feature
9. Client Monitoring App Enhancements
- Added tracking joystick motion as well as DCC motion
- Added option to resize dashboard tiles
- Fixed: DST issue in utilization calculation
10. Other Enhancements
- [1] Added new operation to allow sending I++ DME commands directly
- [2] Added Construct Point - intersection of (curve) cloud and plane/line
- [3] Allows to open associated program operation from Feature dialog
- [4] Keeps Furniture shown when using Place CAD command
- [5] Changed circular plane size definition from radius to diameter
- [6] Allows to set VB Script variables via command line argument - [7] Project revision history is now saved in file with optional comments
- [8] Improve ISO 10360 Probing Test - Allows to retrieve/input temperature info - Allows to output raw data
11. Driver Updates
- B&S Sharpe2 - COM port communication issue with USB to Serial adapter
- Faro Arm - TP20 trigger not detected reliably on Faro USB Arm
- Mitutoyo UC - Allow smaller pitch for SP25 unknown scan
- Fixed SP25 calibration output not scaled to Scale Factor
- Fixed software crash upon connection due to unexpected PHC response
- UCC Direct 2.0 - Fixed failure to send tool offset to UCC when re-connecting
- UCC I++ - Fixed software crash when doing I++ Sync with UCCserver that contains incompletely defined tools
- UCC Manual - Add support for UCC manual controller (MMI-2)
- Zeiss C99 - Allows to set joystick backoff distance
12. Bug Fixes
- [1] Edge/Angle points did not simulate or verify when using the simulate/verify function
- [2] Edge Point could show false error "two vectors are not perpendicular"
- [3] 2D scan feature location should not be projected to working plane
- [4] Edge Points in Points page sometimes did not snap points to the nearest edge
- [5] Probe Assembly dialog always shown in 3 decimal places even for inch
- [6] No verify button for Manual Measure Hole Pattern
- [7] Furniture did not stay hidden across sessions
- [8] No prompt to save project file upon closing with changes made to graphical report
- [9] Probe display incorrect during probe change (higher than it is)
- [10] Operation dialog shown on main monitor when CMM-M was running on second monitor
- [11] Help desk file export did not include files in all subfolders
- [12] Line-Circle intersection did not display points when axis line was used
- [13] Re-Boundary CAD surfaces on some models could cause software crash
- [14] Exported DXF Curves could not be opened in Fusion 360 / Autodesk
- [15] Not all features translate after cut/paste
- [16] Certain STEP model dimension became much larger when imported
- [17] SP25 scan program execution could use wrong approach and backoff distance
- [18 ]Selecting multiple features for construction may cause software crash
- [19] Wrong T deviation output when actual and nominal ref. frames were different
- [20] Homing in SFL without configuration file would cause the software to freeze
- [21] Certain Construct Point operation in a program could cause software crash upon file close
- [22] Failed to close programs with collapsed Program Groups containing disabled Get Probe Assembly operations
- [23] Default Vision layouts included incorrect DRO window
- [24] Error constructing mid-plane of two circular planes
- [25] Construct Bestfit Plane probe comp direction could be wrong when PCS Z-axis was inverse of nominal plane direction
- [26] Convert Excel to CSV may fail due to non-existent cached file path
- [27] Gasket scan not working properly in INCH mode
- [28] Ellipse fitting issue with probe comp
- [29] Background was not white when printing the display window
--End